Turbulent times increase importance of rapid delivery of construction projects
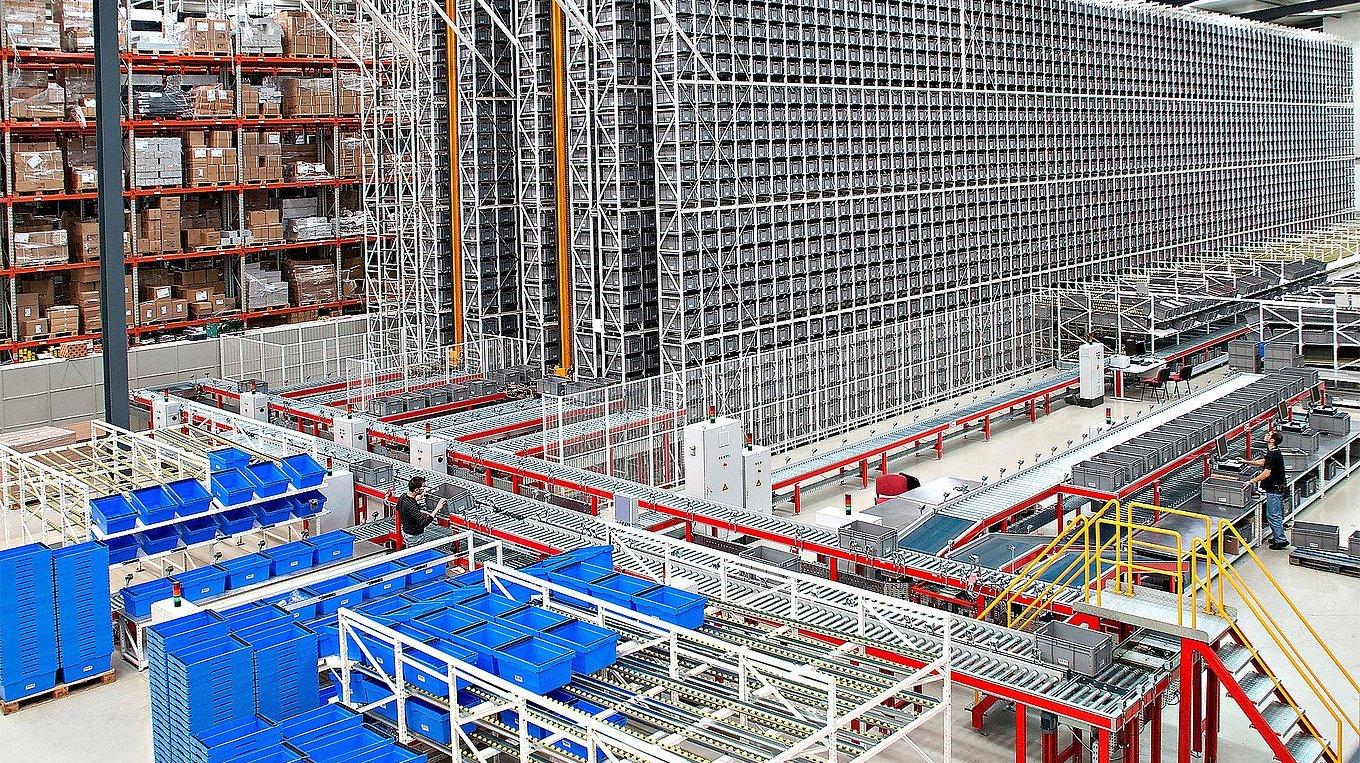
Back in 2020, I discussed the impact COVID-19 was having on food and drink manufacturing construction projects, as the pressure to deliver on deadline was exasperated by the regulations and restrictions of lockdowns.
While the restrictions from COVID-19 crisis have eased, certainly in the UK and Europe, the construction sector’s hopes of recovering and making up for lost time have been met by a multifaceted web of challenges which is increasing the need for rapid delivery of construction projects.
What is driving the rise of rapid delivery of construction projects?
With inflation leading to huge fluctuations in the cost of materials and a shortage of labour increasing wages, not to mention new lockdowns in Asia, and of course further delays due to the ongoing war in Ukraine, many construction projects are caught in a perfect storm of increasing costs and complex supply chain issues.
The Building Cost Information Service (BCIS) Materials Cost Index has predicted that the cost of raw materials is expected to treble in 2022, having already increased fivefold during the COVID-19 pandemic. The BCIS Material Cost Index is now forecast to reach 17.5% by the end of 2022.
To add another complication, Russia’s invasion of Ukraine has amplified fears of global inflation and rising interest rates. This could result in a period of stagflation, a drop in output alongside a prolonged period of inflation. Although inflation is hitting all industries at the moment, with construction margins squeezed, the viability of some projects could be called into question.
The war in Ukraine is also having a more direct impact on the cost of materials, with both Russia and Ukraine major suppliers of metals, raw materials, chemical products and machinery, including oil and natural gas, as well as copper, nickel and platinum.
Rapid delivery of domestic projects
The global supply chain crisis is only set to intensify, with shipping costs from Asia already at record highs.
These ongoing supply chain disruptions, alongside the need for businesses to reduce their impact on the environment, are leading to a rise in food and drink manufacturers restructuring their supply chains to a more localised model. This process of ‘near-shoring’ supply chains involves major new construction projects, with factories needing to be built in domestic locations.
Operating in an increasingly unstable and unpredictable geopolitical environment, alongside rising commodity prices and shipping costs, food and drink manufacturers know that speed is a key factor when completing new projects.
This is certainly the trend we are seeing at IFP Construction, with a rise in demand for the rapid delivery of the design and build of food and drink manufacturing plants in the UK.
At IFPC, we have vast experience of completing accelerated programmes of delivery in complex and live food environments. Not only do food and drink manufacturers benefit from quickly shifting to operating from new, localised factories with shorter supply chains, but our transparent contracting approach to costing means that many prices for materials can be agreed and ‘locked-in’ early, avoiding lengthy tendering processes and reducing the impact of the uncertain global marketplace where costs are rising all the time.
The COVID-19 pandemic delivered a sudden shock to the food and drink manufacturing sector, and as the world kicks into gear again, we are facing a new set of challenges. Business leaders in the food and drink manufacturing sector know they need to take action, and the long-term benefits are without question, but ensuring a swift and smooth transition to new factories with alongside controlling costs, will be of the upmost priority.
Matt Sparrow – operations director at IFP Construction